
Voici un morceau de poutre en U pris dans les chutes de l'entreprise
qui m'emploie. Section 120 x 50 mm
(environ). Epaisseur des parois 8 à 10 mm
selon l'endroit. Le voici sous la scie. Dans la bouteille, du lubrifiant
de coupe (pas du pastis, hein!). Il va être
ramené
à une longueur de 400 mm et je
vais pratiquer deux saignées
sur les petits côtés. Ces
dernières seront
à 50 mm du bord.

Voilà le résultat.
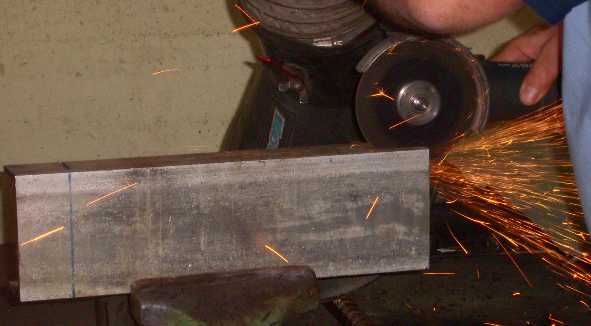
Ensuite il s'agit d'enlever les petits côtés sur
350 mm
(ben oui 400-50!). Je voulais le faire avec la
scie de ci-dessus (Devos?) mais on m'a
prédit beaucoup d'ennuis. Le gentil Guy a proposé
de me
le faire à la meuleuse
d'angle équipée d'un disque à
tronçonner
(parce que je suis gentil parait-il).
Effectivement ce fut très
rapide. Prévoir au moins 2 disques (et de
qualité!)

Là c'est du superflu mais Guy ne m'a plu
lâché. Il
a dit que cela serait plus propre comme cela. J'étais
pressé (et encore une fois cette
opération
ne sert à rien pour la fonctionnalité du
support), mais je
suis
aussi poli alors je n'ai rien dit. Cela avait l'air de lui
faire plaisir. En clair avec une fraiseuse verticale munie
d'une fraise 2 tailles, on
reprend un peu les traces laissées par la meuleuse.

Ces "oreilles" ne sont pas assez longues pour prendre appui sur la
transmission finale.
Pour les rallonger je veux y souder 2 morceaux de fer plat. Afin de
bien garantir leur position,
on usine deux petits épaulements sur les faces internes des
"oreilles" (photo floue, désolé!)

Vient ensuite le perçage des 4 trous qui serviront
à
fixer la transmission. Ils doivent tomber en face
des trous de fixation de la roue. Leur centre est sur les 4 sommets
d'un carré de 48 mm de côté.
Afin de laisser un peu de liberté au montage, les trous sont
percés à 13 mm (vis M12). Les 2 trous
les plus proches des "oreilles" sont à 167 mm du bord
(côté "oreilles"!). La machine outil ici est une
fraiseuse à commande numérique (elle
était juste
dispo à ce moment) mais une bête perceuse ferait
très bien l'affaire.

En parallèle, j'ai coupé deux morceaux de fer
plat. Ils
font 70 X 50 X 8.
Voici tous les composants au poste de soudure (TIG;
également
parce que dispo).
Tout poste de soudure à l'arc conviendra bien sûr.

Les petits épaulements en détail. Ne surtout pas
supprimer le congé par soucis esthétique.
Il ajoute énormément de résistance
à la
flexion des "oreilles".

Voilà les cordons de soudure. Espérons qu'ils
soient
suffisamment gros et solides.
En prime, le rappel de la distance bord-trous de 167 mm.
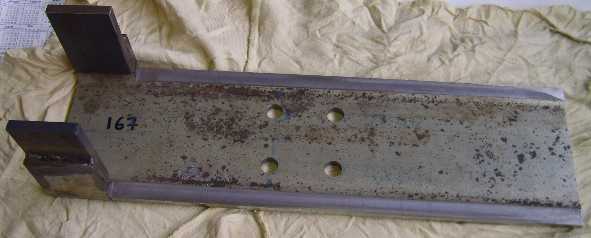
Voilà la pièce finie. La partie à
droite des trous
doit être prise dans l'étau pour le maintien de
l'ensemble.
Quel est l'effort qui va s'exercer sur
les
"oreilles"? Les rapports de réduction des
Béhèmes
vont de 2.75 (K1) à environ 3.3 (850 cm
3).
L'écrou se serre à 200 mN. On
récupère donc
200 X
3.3 = 660 mN sur la couronne. La distance centre de la couronne-point
d'appui sur "l'oreille" est de 166 mm soit un effort de 660/.166= 3976
N soit l'équivalent de 405 kg!
Sueur froide: au démontage,
il faut exercer
bien plus de 200 mN pour desserrer l'écrou (frein de filet
très fort!). Le fragile carter en aluminium tiendra-t-il? Ne
s'écrasera-t-il pas comme une vulgaire m****?
La
fabrication d'une douille à ergots est en page
2.
La
fabrication d'une douille de montage d'un joint "spy" est en page 3.